Organization: Actually Important for Engineers [and Everyone Else]
Your office may be messy, but you had better know where your tools and parts are. Better yet, someone else should know where they are!
So a post about storage… You’re probably about to swipe left1, but maybe this is actually worth your while. Or maybe not, you could be doing something better with your time, such as watching AI Will Smith eat spaghetti.2
So why does organization matter in the tech/engineering adjacent space? And why should you listen to me on the subject? If the rumor is true, my cubicle was once (at least once) singled out as a the bad example for the company’s 5S3 efforts.
Nevertheless, today I spend a significant amount of time organizing my parts and tools. Think of this article as a sort of Scared Straight documentary from a lifelong messy person.
First, let’s cut to the chase:
Why organize/clean?
Save time in the future - You don’t have to root around for part tool X, Y, or Z (over and over again).
Save expense buying new tools/parts - You actually have the thing X that you bought and don’t have to buy a new X.
Save TIME AND EXPENSE - You can easily find X instead of searching around for it and then still buying it
Floor space = 💰 - as of 2024 the average cost for home floor space in the US is $233/square foot. What is the cost of that thing if you add in this expense? Should a trash can really cost ~$500?
Ready to Make! - When you have an idea and things are clean, you can get started ASAP, rather than cleaning first. Put in the work now, be ready later!
How to organize
Eliminate - Toss what you don’t need–make finding easier and save floor space
Think vertical - Floorspace costs money. Stack things on top of each other and you’re dividing out this cost.
Label - E.g. reading the box is much faster than opening the box. This is especially important if multiple people will be searching for something.
Custom storage via 3D printer - So many possibilities. See below
Establish an organization system
I put a lot of time, effort, and money into keeping my workspace organized. In fact, if you look at my Printables profile, my top 3D-printed designs are for organization. I also built a garage bike/stuff storage system 👇 that took a lot of effort, but helps keep things manageable.
At the same time, things in my garage and office are not always tidy, in a large part because I haven’t properly put things away, even if they go somewhere. Whether for yourself, or (especially) for a business, you should first establish a system for storage and organization, then put things in place. Otherwise you’re just stuffing things in drawers ➡️ unseen, but still messy.
Of course, if you’re responsible for a manufacturing line or industrial/company facility4 you can often take things up one more level organization-wise:
Fully automate organization: use… the crib🚀 [industrial]
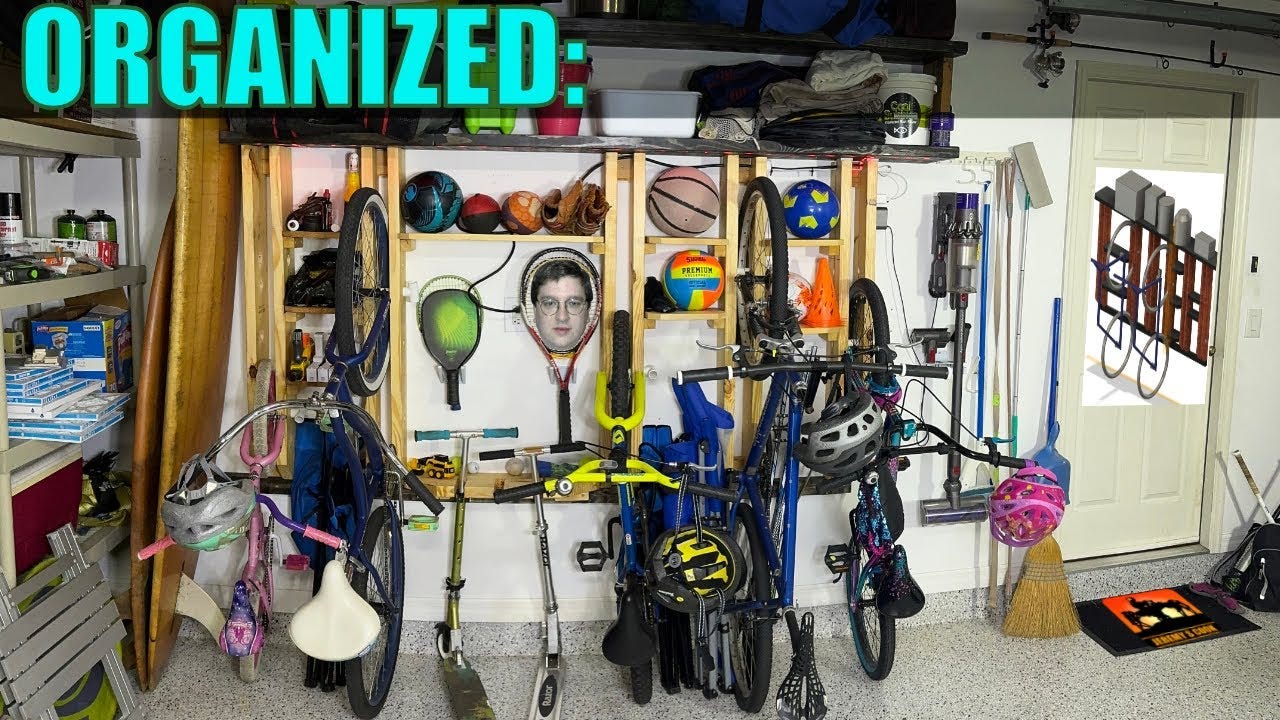
If you work for or own a larger company (i.e. more than just you), you may have access to an internal storage area known as a crib.5 This area generally has one or more attendants to keep things organized, and tracks parts and tools on hand and reorder things as needed.
While this may seem uninteresting, “the crib” can actually be an amazing tool in the fight against machine downtime and engineering hassle. Imagine you have 10 technicians depending on you, and you keep all spare parts in your office. They will bug you each and ever time they need something, and if you don’t have said part, there’s a mad scramble (by you) to get it. They also may keep spares in drawers and toolboxes in the workshop area… which are inaccessible and/or unknown by all but that person when needed.
The solution: put critical spares in the crib. Typically you fill out a form and things are kept there and reordered automatically. No secret spares, not clutter in your office, no panic if something isn’t available… it’s someone else’s job.6
Not only does this save YOU hassle as an engineer, also it keeps the factory running smoothly when parts are needed. Parts expenses can also be reduced, because a spare can be kept in one place, rather than four spares spread throughout your shop.7
I’ve personally put hundreds of items in cribs at different manufacturing facilities–which kept me more sane than I would have been otherwise–and this ultimately benefited the company. Philosophically, engineers should focus on establishing a framework for success (i.e. automated organization) versus dealing with each and every little problem (i.e. parts stored in your office).8
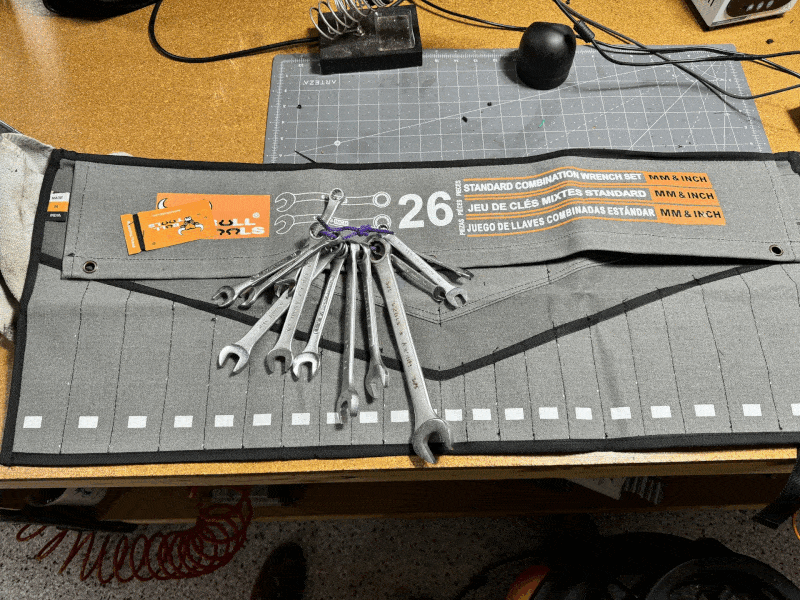
The future of organization: databases and… robotics? 🤖
Where do I see organization going in the future? How about a system where you photograph an item going into storage, and it is automatically cataloged for searchability (e.g. “find a black wrench”). This could then point you to industrial-style crib locations (at home or in industry). Taking it a step further, such a storage database could even match images of beaten-up parts with their pristine replacements.
The tech is here, it would just be a matter of putting everything together. On a personal level, a smartphone-based family database might eliminate some hassles… but good luck getting that implemented properly.
What about a robot to clean up after you? If you were to have all your stuff in a photographic database with designated locations, then a robot could, in theory, pick up after you and put things in the right spot. As discussed in the It Can Think! post below, a company just came out with a Roomba-like robot con manipulator that can presumably, sort-of, pick up after you.
The catch? It costs around $2000 and the manipulator itself isn’t particularly impressive. Never say never, but it will be a while before a robot comes and picks up your dirty laundry, washes it, folds it, and puts it away. For the time being, robot cleaning will be more akin to the maid that you tidy up for before that person performs more generalized duties like sweeping, mopping, and dusting.
Still, one can dream of a day when you can set up your cleaning system to have it take care of the mundane day-to-day tidying for you!
Here’s to a clean and organized future! -JC
Thanks for reading! I hope you will follow along as I post weekly about engineering, technology, making, and projects. Fair warning: I am a native Florida man, and may get a little off-topic in the footnotes. Maybe I even had an alligator or two as pets growing up. Perhaps they are alive today and could be used to test earth-wormhole pet friendliness.
Any Amazon links are affiliate
Addendum/Footnotes:
Or swipe right? I’m not actually sure. I met my wife in actual, real life, when online dating was still in the “what you met your spouse online???” realm. But I think swiping left means moving on to check out someone else (or something else) in this case. Is the current dating scenario better or worse today than it was when “you met your spouse in person???” became abnormal? I’m not sure, but I’m glad to be out of that particular game.
Yes, that’s AI. Scarily, it’s hard to tell, but wait for the hamburger part and observe the weird bite out of the bun. As for AI in the music realm, check out this post.
I kept lots of parts and things I was working on on my desk because, well, I needed to work on them. One of the people running the effort then took a picture of my desk and plastered a huge image of it in a frame as “bad example.” Who knows, maybe it is still there.
And for those that haven’t been through it, 5S stands for sort, set in order, shine, standardize, and sustain. Some of it is very good, some of it can be taken to an extreme.
You might note that warehouse storage a la Amazon is not really broached in this article. One might argue that such companies sell offsite organization at a massive scale. Perhaps that’s a story for another time, but I included an appropriate video below for your entertainment. On a much smaller scale, one crib that I worked with (which was operated by a different company on-site) actually used a system of vertical bins that moved into place for retrieval. Pretty cool use of space.
My engineering experience takes place in the Southeastern United States. Is “crib” a colloquial term–similar to how one might refer to a motor wiring box–or is it more officially established lingo? Let me know your thoughts in the comments!
Until something goes wrong and you find it is ultimately your responsibility, if not your fault per se.
Working at a bearing factory out of college, much of the “FA” tooling that I worked with was already established in our crib thanks to my predecessor. He told me that this was quite a hassle before because if something was missing (or broken) from the untracked storage area it was his responsibility to find it or have it made.
I was also over “FB” tooling and when I established storage in the crib it meant not just a load off of my back, but cleaning out cabinets with outdated or redundant tooling. If you can throw stuff out, plus set up automated storage at the same time, that is a huge win.
Eliminate missing parts hassles early on so you can start to make real improvements in your product lines. Such work is much more interesting than dealing with everyday emergencies in my opinion, though I guess you may seem more “needed.”
OTOH, if you’re running around heroically, solving problems that you should have prevented earlier, management may see this as a positive. But you still have more stress to deal with!
Jeremy, we need to have a phone call about the alligators (for a story I'm writing)!